Why Your Facility Needs Its Own “Google Street View” for Operations
"Aetos is like using Google Street View in my facility - except way more helpful."
That was what one of our users shared a few weeks ago, and we loved the way he explained it.
In this month's blog, we present a unique idea: similar to how visual navigation with Google Street View is intuitive and immersive, what if we could give that same experience to technicians and operators within their own plant?
What would that do for a facility?
How would that change daily operations?
Could this enablement really change the way workforce personnel experience tasks, troubleshooting, and training?
Ready to see your facility in a whole new dimension — literally?
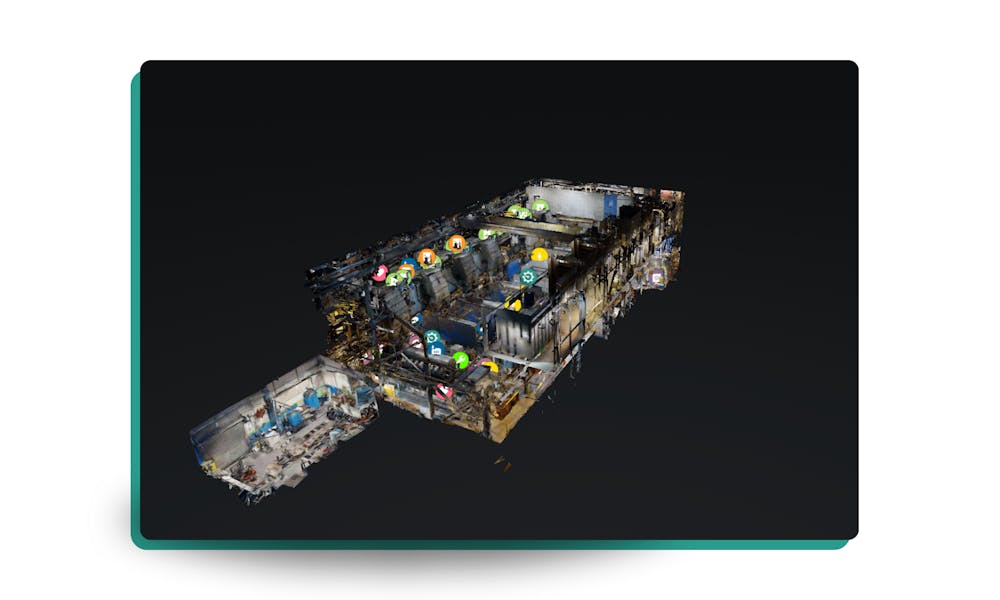
Visual Context Is More Necessity than a Luxury (but it's both)
We lean on visual tools to make faster, smarter decisions.
We don’t unfold paper maps anymore. Instead, we use digital visuals that allow us to zoom, orient, and act.
When you're heading somewhere new, Google Street View tells you what to expect before you ever arrive.
Aetos is the same way.
Yet when it comes to industrial and commercial operations, we still expect workers to function without that kind of clarity. Floor plans are flat, photos are disconnected, and asset information lives in too many places. This makes everyday problem-solving slower, more error-prone, and more frustrating.
The Problem: Operational Blind Spots
Despite massive investment in digital tools, most facility teams are still operating in the dark. Information is siloed. Technicians rely on memory, tribal knowledge, and stacks of inconsistent documentation.
Training happens in conference rooms, far away from the real-world complexity of the production floor.
Even basic tasks – like finding a valve or confirming the right breaker – can require phone calls, digging through files, or wandering the facility. The more complex the system, the harder it becomes to navigate without guidance.
And when seasoned workers leave, that critical site-specific knowledge often goes with them. The cost? Lost time, compromised safety, and inconsistent results.
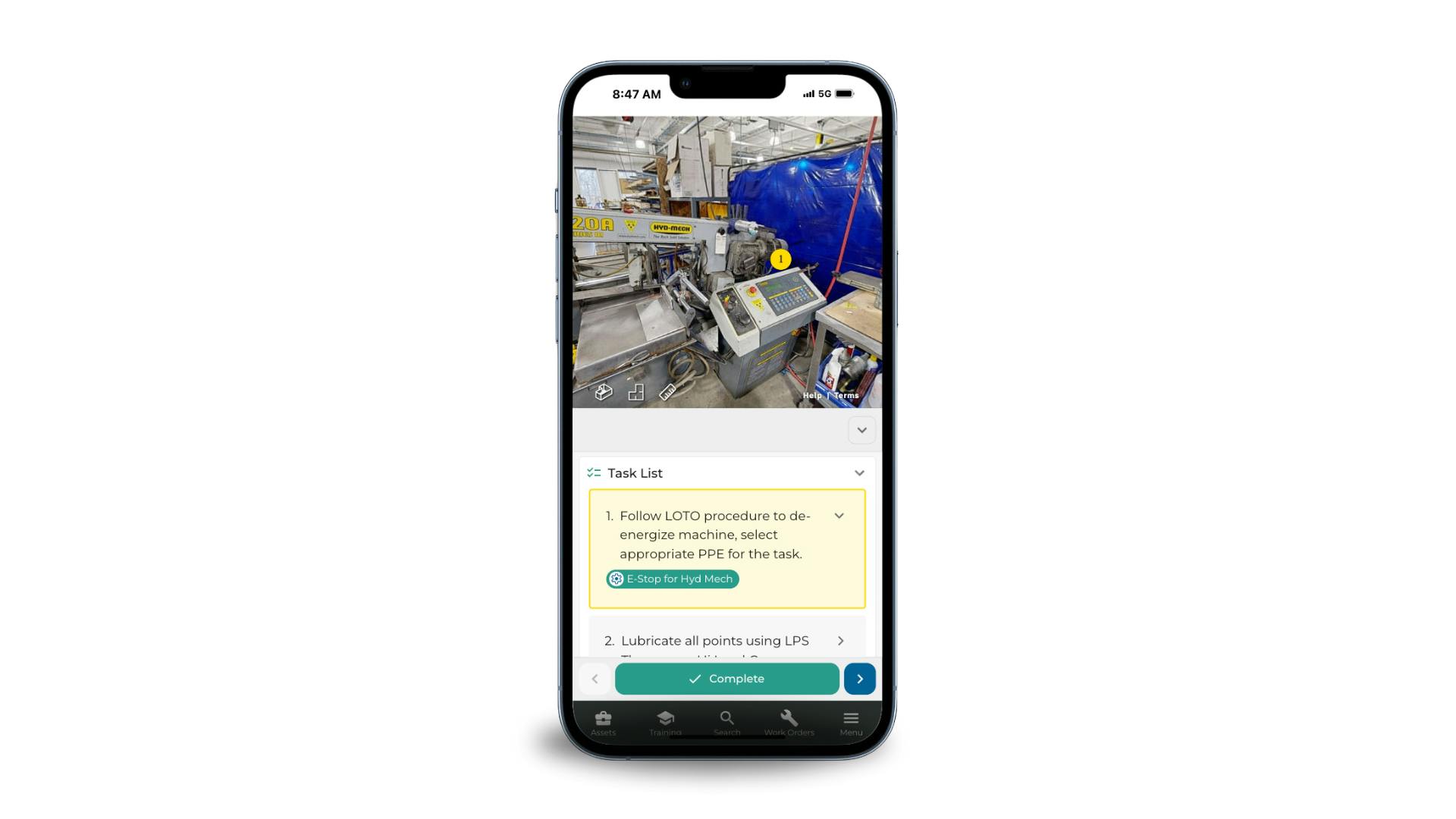
The Opportunity: A Digital Window Into the Physical World
Imagine if your team could virtually walk your facility (from control rooms to rooftops) with just a few clicks.
Zoom in on a pump.
Tap to access maintenance logs.
Click to play a step-by-step video from the manufacturer.
Or pan around to see upstream and downstream components.
This kind of visual interface makes complex environments feel intuitive. It creates a shared understanding between teams, even across shifts or locations. It also turns any device into a portal for real-time knowledge.
Whether you’re on-site or remote, your facility becomes accessible, explorable, and navigable.
From Task Execution to Total Visibility
With a visual-first experience, your workforce gets to complete tasks and understand them.
That leads to:
- Faster onboarding with immersive, site-specific training
- Easier troubleshooting when teams can visually trace systems
- Stronger compliance and safety, with SOPs layered directly into the environment
- Less downtime due to improved awareness of surrounding assets and configurations
And beyond efficiency, this also creates ownership. When workers can see how their actions impact the larger system, they feel more connected to their role. That context drives better decisions, stronger engagement, and fewer errors.
Every facility has quirks and inefficiencies like unlabeled valves, workarounds, missing signage, or custom processes passed down verbally.
There's risk with these types of gaps: Best practices and efficient operations that could be digitized and passed on actually leaves when your people do.
A visual operations platform captures and standardizes these nuances so they don’t disappear. Your facility becomes teachable, sharable, understandable, and future-proof.
It allows teams to annotate, layer in SOPs, and document context around every asset: not just what it is, but where it is and how it’s actually used.
As a result, every task becomes repeatable and scalable. Your processes aren’t both documented and experienced. That’s how institutional knowledge becomes institutional memory.
Your Facility: Digitized, Visual, and Available
What Google Street View did for cities, our visual operations platform can do for your facility. Aetos makes your environment explorable, your workflows clear, and your workforce confident.
It’s time to stop managing your operations with outdated PDFs and start giving your team the modern tools they deserve. Welcome to the visual revolution (a close cousin to digital transformation).
With every scan, you’re building a smarter, more connected workplace. This is more than a technology shift; it’s actually a mindset shift for your current and future workforce.
So fold up those maps and roll up your sleeves because the future of work, training, safety, and procedures isn’t flat – it’s immersive.